Troubleshooting: mold making project for nylon molded parts
Last year we have made 2 sets of injection molds for a US company, the part we are going to mold is made in nylon, also called PA6, it looks like a simple part, but in actual practice, a few problems comes up, our specialists solved it eventually, it is supposed something we can learn and share.
Here are a brief idea of the injection mold and nylon part:
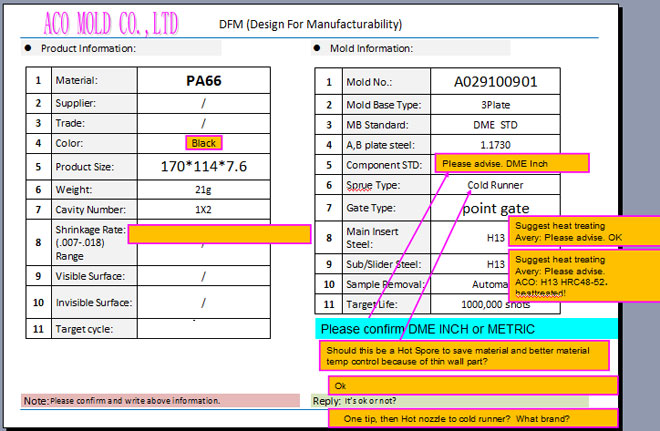
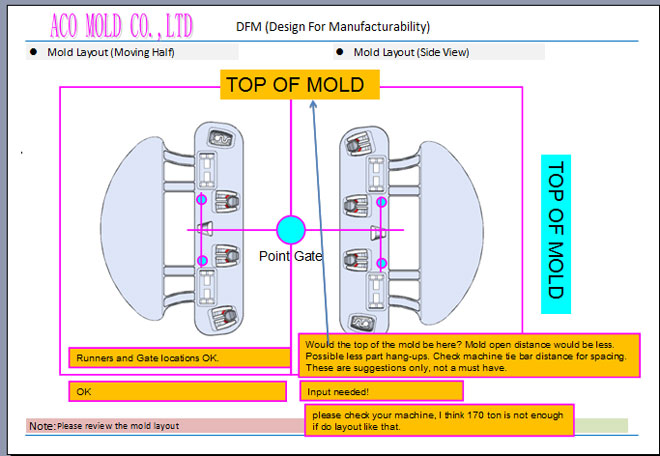

As you can see the part is just a slim plate, the mold cavity side need to be sandblast and there is nothing to attach to core side, we need to make sure the nylon part will not stick on cavity side during injection molding, so sucker pins are needed on core side, the customer propose to make 2 sucker pins only at the beginning, but actually it turns out not enough, see the picture of T1 test, we got the parts stick tightly on cavity side, the problem was solved by adding 2 extra sucker pins later after.
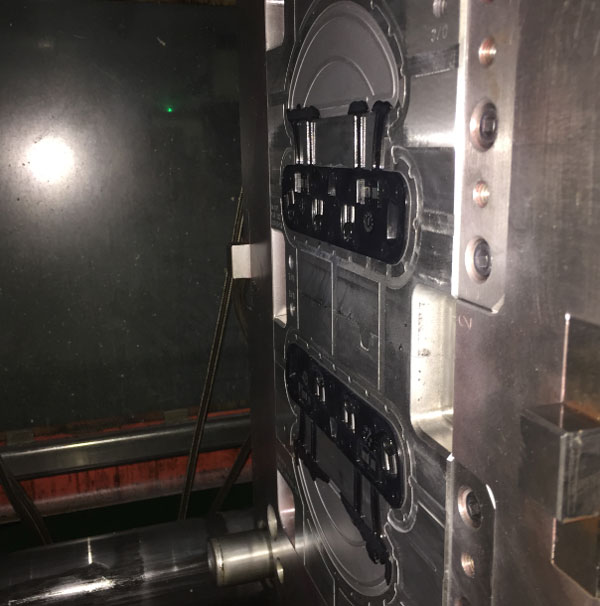
Another problem is the surface defects, we had some shinning marks on the nylon parts, see the T1 samples (2 parts in the pictures were flip over, ejector pins all over it)
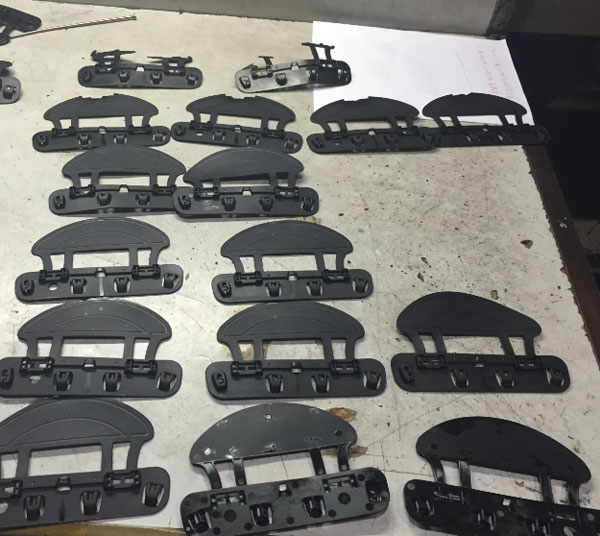
Gate for parts made in PA6 material gets cooled down and sealed off fast, so it is very easy to have some surface defects around the gate, to make it right, a few things you may want to check: if resin were dried out completely, proper mold temperature, high injection speed etc.
Here are the final approved samples and see the clean shut off area, No flash at all!!!!
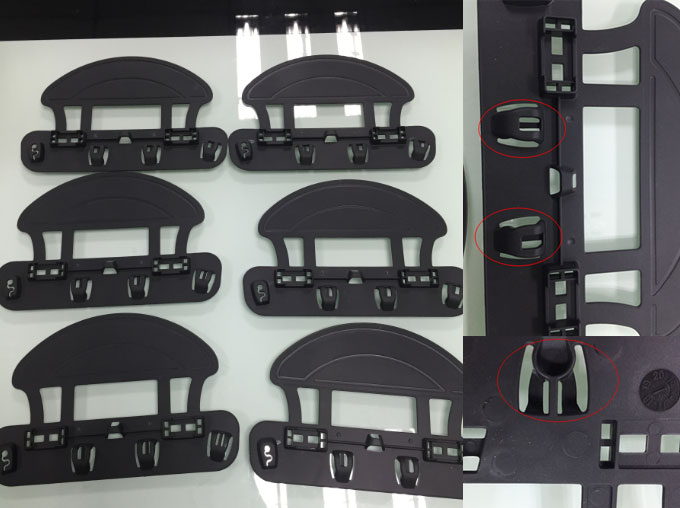
Aco Mold have very strict standard procedure for all injection molds coming out of our factory, after the samples are approved by customers, all molds will be set up for a few hours running to confirm stable production situation so all molds arrive at customer's factory can gets right into smooth production.
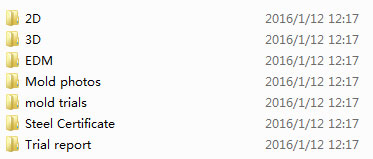
Along with the injection mold, we provide full packages of all documents, including 2D mold design drawing, 3D mold design drawings, DEM cooper, NC programming data, disassembled mold pictures, injection molding parameter report, mold test video, steel certificate etc.
Here is how the mold looks like before shipping, we check and clean every piece of the components before we packed them.
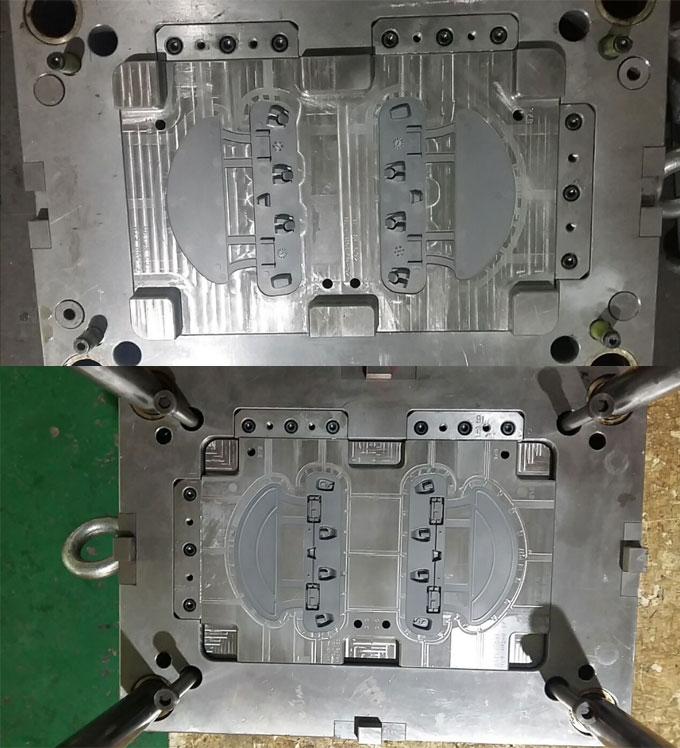
Here is the steel certificate, please note all the steel we used are from LKM, the biggest mold steel/mold base vendor in Asia, all the steel we purchased and used can be tracked on LKM's website.
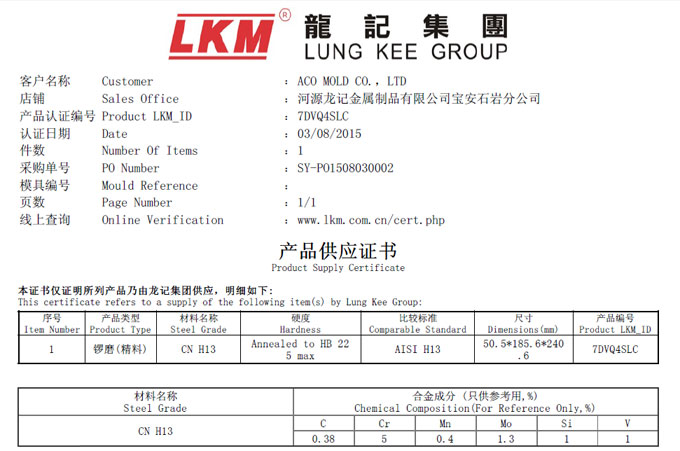
And the mold test video
Here are a brief idea of the injection mold and nylon part:
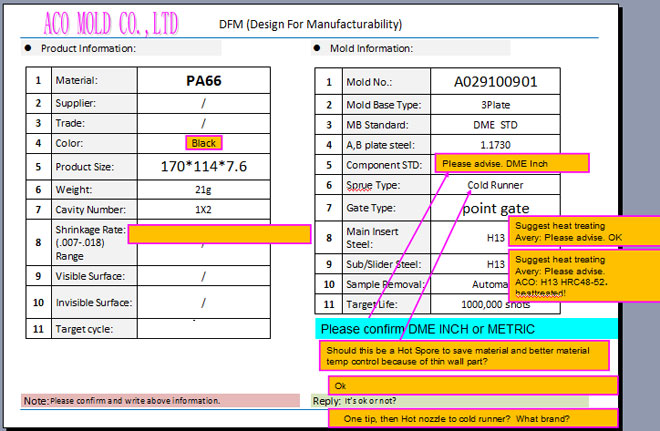
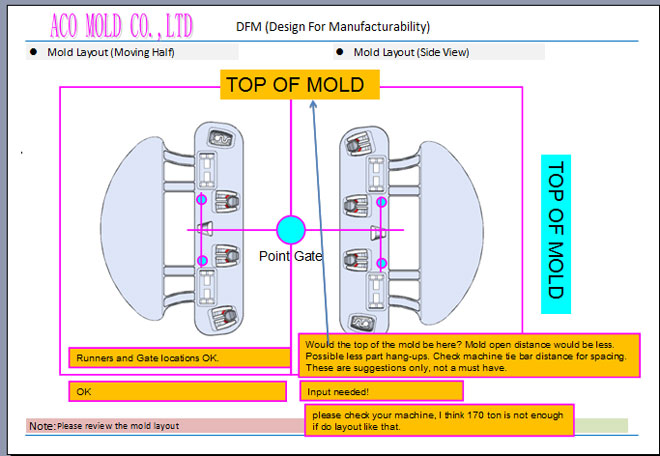

As you can see the part is just a slim plate, the mold cavity side need to be sandblast and there is nothing to attach to core side, we need to make sure the nylon part will not stick on cavity side during injection molding, so sucker pins are needed on core side, the customer propose to make 2 sucker pins only at the beginning, but actually it turns out not enough, see the picture of T1 test, we got the parts stick tightly on cavity side, the problem was solved by adding 2 extra sucker pins later after.
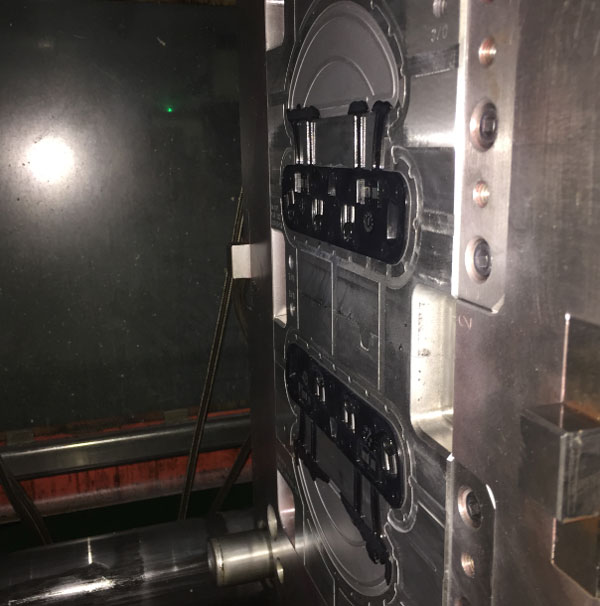
Another problem is the surface defects, we had some shinning marks on the nylon parts, see the T1 samples (2 parts in the pictures were flip over, ejector pins all over it)
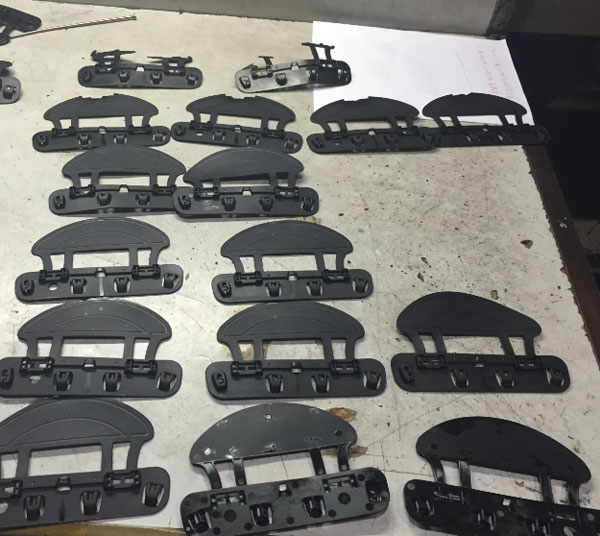
Gate for parts made in PA6 material gets cooled down and sealed off fast, so it is very easy to have some surface defects around the gate, to make it right, a few things you may want to check: if resin were dried out completely, proper mold temperature, high injection speed etc.
Here are the final approved samples and see the clean shut off area, No flash at all!!!!
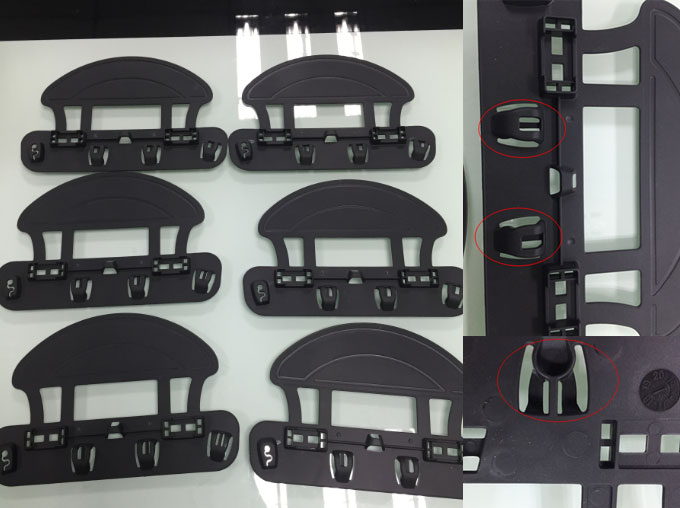
Aco Mold have very strict standard procedure for all injection molds coming out of our factory, after the samples are approved by customers, all molds will be set up for a few hours running to confirm stable production situation so all molds arrive at customer's factory can gets right into smooth production.
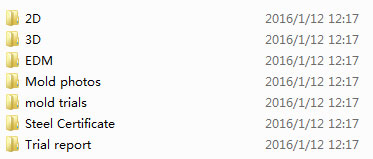
Along with the injection mold, we provide full packages of all documents, including 2D mold design drawing, 3D mold design drawings, DEM cooper, NC programming data, disassembled mold pictures, injection molding parameter report, mold test video, steel certificate etc.
Here is how the mold looks like before shipping, we check and clean every piece of the components before we packed them.
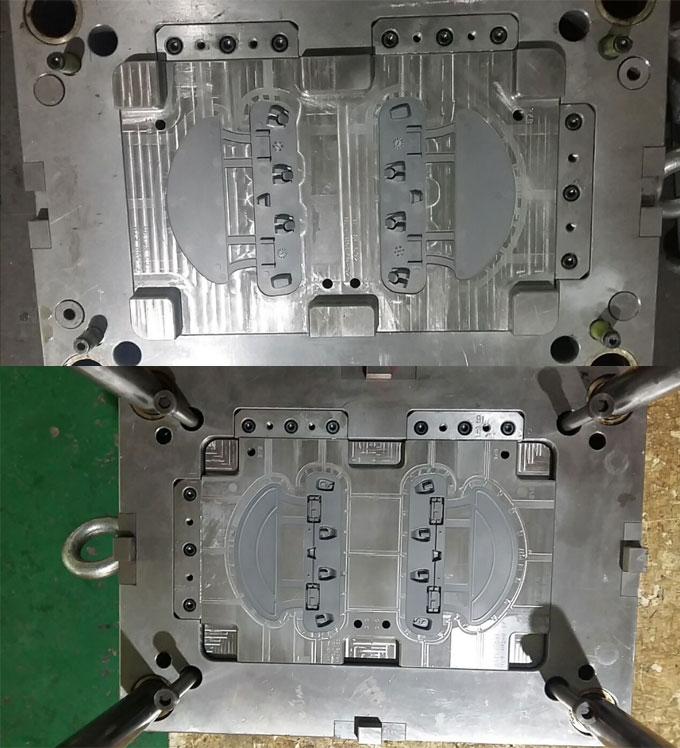
Here is the steel certificate, please note all the steel we used are from LKM, the biggest mold steel/mold base vendor in Asia, all the steel we purchased and used can be tracked on LKM's website.
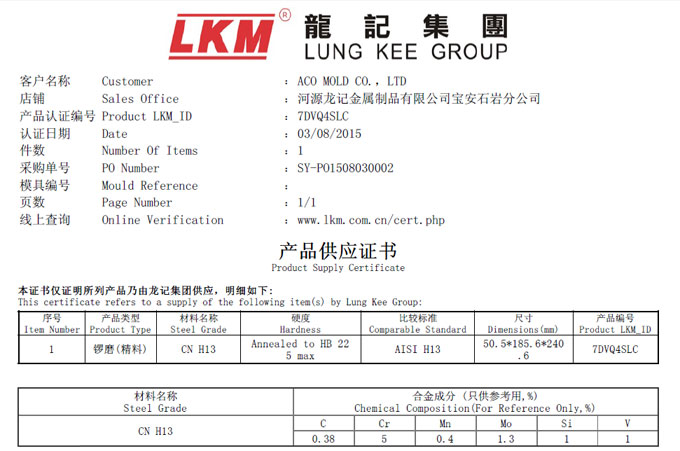
And the mold test video