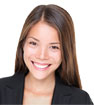
Mold Manufacturer China

Home » "How To"
The major reason that American and European companies source plastic injection molds in China is price, at the end of the day that is the major factor. However if we want to have a feel good discussion and ask what to look for when selecting a Chinese injection mold supplier we can look for the following:
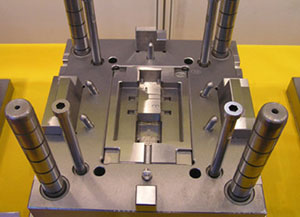
- References -- Get it from them and do your homework
- Origin of Tool Steel
- Capital investment in shop and equipment -- Is it a dive?
- In place (established method) project plan that shows every aspect of build and give updates
- Quality Systems
- Validation Systems
- Knowledge of your product -- Have they done this before?
- How much capability do they have -- Can they do everything in-house?
- Capacity and what is it at the moment you are placing your P.O.
- Are they able to service you globally?
Injection mold manufacturing is a very complicated process, from the steps of initial design, processing, assembly, mold trial, etc. to the final mass production. During the entire life cycle, we must take into account effects of each manufacturing process on the quality of injection mold. And concern every detail to improve the quality of injection mold.
With injection molding and machine using both are indispensable. The operation of mold injection is actually accomplished by operating the injection molding machine. The correct use and maintenance of the mold is an important factor in ensuring the continuous production of high quality plastic products and extending the life of the mold injection molding. Using and carefully maintaining injection molding correctly is of great importance to maintaining normal production and improving company benefits. Then pay attention to several aspects.
How to evaluate the mold factory level of technology? The final performance in the mold manufacturing cycle, mold life, mold accuracy and rigidity, mold manufacturing costs, mold standardization and other aspects. These are the basis for plastic mold manufacturers in China to evaluate the economic and technical indicators of the mold.
How to choose reliable injection molding manufacturers? This question is believed to be of concern to many companies. A reliable injection molder supplier is not only a guarantee of product quality but also a solid backing for product production cycle and stability. Therefore, most companies will have a relatively long inspection period when they choose an injection mold factory. How can one judge the selection of such a company?
Mold trail refers to, in the product development and manufacturing, the test injection step that is carried out after the mold making is completed and before the mass production.
In order to avoid unnecessary waste of time and trouble, it is indeed necessary to pay patience to adjust and control various processing conditions, and to find the best temperature and pressure conditions, and to formulate standard test procedures, which can be used to establish Daily work methods.
Record and analyze data which is used for the need of modifying molds and production conditions, and providing reference for future volume production.
At present, the mold temperature is often neglected during the test of the mold, and the mold temperature is the least easy to grasp in the short-term mold test and future mass production. The incorrect mold temperature can affect the size, brightness, shrinkage, rhythm and under-charging of the sample. If you do not use a mold temperature controller to grasp, the difficulties will occur in the future’s mass production.
In order to avoid unnecessary waste of time and trouble, it is indeed necessary to pay patience to adjust and control various processing conditions, and to find the best temperature and pressure conditions, and to formulate standard test procedures, which can be used to establish Daily work methods.
Record and analyze data which is used for the need of modifying molds and production conditions, and providing reference for future volume production.
At present, the mold temperature is often neglected during the test of the mold, and the mold temperature is the least easy to grasp in the short-term mold test and future mass production. The incorrect mold temperature can affect the size, brightness, shrinkage, rhythm and under-charging of the sample. If you do not use a mold temperature controller to grasp, the difficulties will occur in the future’s mass production.
Introduce the mold quality effect factors , the basic ways of mold quality improving, and typical cases in using right methold and maintenance.
Even if is very professional and have rich experience in plastic mold processing, also can't guarantee the production of plastic is one hundred percent qualified, more or less has some processing defects. But these defects can be controlled and life of the mold can be improved.
If you plan to make molds outside of the United States, and you don't have an international patent. Remember you have no legal means of stopping someone in China from building a second set of injection molds and producing your product and selling it in say Australia, Japan or Europe, quite possibly before you roll it out in the United States.
A lot of problems come from communication and working habits from my experience actually. Many injection mold manufacturers in China can't speak and listen English very well, it may be the biggest reason of causing some problems. If communication no problem, Chinese manufacturers are very much willing to do everything possible for their customers.
A lot of problems come from communication and working habits from my experience actually. Many injection mold manufacturers in China can't speak and listen English very well, it may be the biggest reason of causing some problems. If communication no problem, Chinese manufacturers are very much willing to do everything possible for their customers.
Warpage is usually caused by molded-in stresses. The issue of warpage is related to being a semi crystalline material, HDPE, being semi crystalline polymer, will have differential shrinkage along and across the flow leading to warpage. It is difficult to eliminate this problem just by optimizing processing parameter. If use of multiple gates is possible, that might help multidirectional flow leading to lesser warpage.
The two areas that will have greatest affect are injection mold temperature and gating being both location and type. Not knowing configuration or flow difficult to give specific advice, but think of the part on a molecular scale. Imagine the surface of part being interconnected crystals with cooling starting at coldest surface of injection mold which will be multiple points and spreading out in a circular shape all within fractions of a second. You want the coldest surface possible and repeatable and a flow front that fills mold as evenly as possible. The more even the flow front in relation to part configuration from one side across to other and a plastic injection mold surface temperature that is a uniform temperature will minimize warp. There are some design tricks that would also minimize warpage but you may past that point. As to type of gate, as large as possible so you are not adding heat through shear. Also monitor melt temp at nozzle, looking for lowest temp that will enable complete mold fill.
The two areas that will have greatest affect are injection mold temperature and gating being both location and type. Not knowing configuration or flow difficult to give specific advice, but think of the part on a molecular scale. Imagine the surface of part being interconnected crystals with cooling starting at coldest surface of injection mold which will be multiple points and spreading out in a circular shape all within fractions of a second. You want the coldest surface possible and repeatable and a flow front that fills mold as evenly as possible. The more even the flow front in relation to part configuration from one side across to other and a plastic injection mold surface temperature that is a uniform temperature will minimize warp. There are some design tricks that would also minimize warpage but you may past that point. As to type of gate, as large as possible so you are not adding heat through shear. Also monitor melt temp at nozzle, looking for lowest temp that will enable complete mold fill.
I was an injection molding trouble shooter for eight years, and in my job today I come across good and bad ones all the time. You can see very quickly which is which I have seen a lot of articles about taking people with boat loads of experience, in principal I would agree, but be cautious that the experience is not blinding the person to think they know it all.
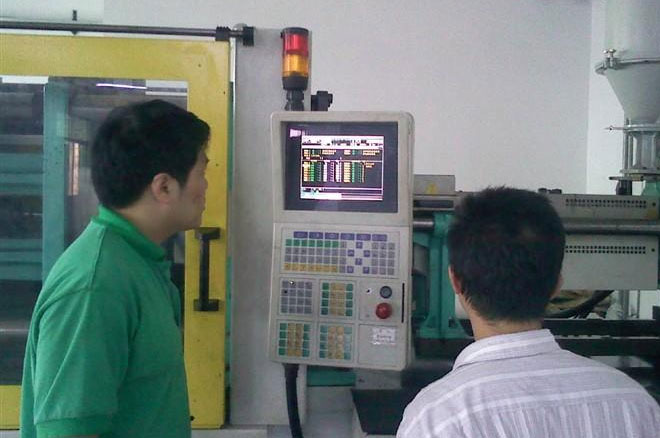
The big part missed is a good communicator. The problem being an injection molding trouble shooter is you can be called in to solve a problem and by fixing it the people originally working on can be put out joint, the trouble shooter can be seen as critic of their work quality. So the best injection molding troubleshooting expert is someone who can work with the people to solve the problem and not need to be seen as the hero taking limelight.
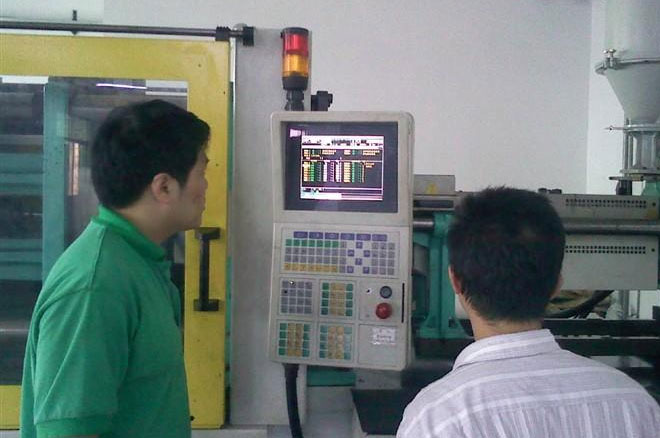
The big part missed is a good communicator. The problem being an injection molding trouble shooter is you can be called in to solve a problem and by fixing it the people originally working on can be put out joint, the trouble shooter can be seen as critic of their work quality. So the best injection molding troubleshooting expert is someone who can work with the people to solve the problem and not need to be seen as the hero taking limelight.
Minimizing of sink marks can be achieved by following proper part design. The sink marks will not be eliminated if you have any ribs or structural features behind the 'A' surface. But with proper part design they can be minimized to a point that they are not visible.
You will never cover sink marks up with the paint, they will appear worse than they do on the plastic part. There are a few good way to check for sink on a part before painting. these are:
You will never cover sink marks up with the paint, they will appear worse than they do on the plastic part. There are a few good way to check for sink on a part before painting. these are:
- Project a grid pattern of bright lines on the part, using an overhead projector, distortion in the grid pattern shows sinks easily.
- Wipe the part with Alcohol and observe the drying pattern. Sink areas take longer to dry.