Parting surface selection of plastic injection mold
The parting surface is for taking out the injection molded plastic part from the mold cavity or in order to meet the needs of plastic molding, such as the installation of insert, and the exhaust. According to the structure of plastic part, the part of the injection molded part is divided into several parts of touch surface. It is divided into horizontal parting surface, vertical parting surface and composite parting surface. When plastic injection molding, in order to facilitate the release of the injection molded part, the plastic injection mold is made into several parts and the joint surface is called the parting surface. When selecting parting surface, try to ensure the quality of the injection molded plastic parts and simplify the processing process of mold making and injection molding. The selection of the parting surface is also the first step in the mold design. It is affected by many factors such as the shape, appearance, wall thickness, dimensional accuracy, and number of cavities.
1. The mold parting surface should be located at the maximum contour of the plastic part.
After the orientation of the plastic parts on the moving mold and the fixed mold is determined, the mold parting surface should be located at the maximum contour of the plastic part, otherwise the plastic parts will not be able to demold from the mold cavity. This is the most basic principle of selecting parting surface.
2. The selection of the mold parting surface should be beneficial to the smooth release of the plastic part.
Since the ejection device of the injection molding machine is on one side of the movable mold, the mold parting surface should be selected to ensure that the plastic part remains on one side of the movable mold after mold opening. This facilitates the operation of the push-out mechanism provided in the movable mold portion. If the ejection mechanism is set in the fixed mold, the complexity of the plastic mold will be increased.
3. The selection of the mold parting surface should ensure the accuracy of the plastic parts and the appearance quality.
The mold parting surface cannot be set on the smooth surface and the appearance surface of the plastic product, so as to avoid affecting the appearance quality of the injection molded part.
For parts where the plastic parts require high concentricity, when selecting the mold parting surfaces, it is best to place them in the same side cavity of the injection mold.
4. The selection of mold parting surface should be beneficial to the plastic injection mold making
Usually in the mold structure design, the selection of the straight parting surface is mostly. However, in order to facilitate the injection mold manufacturing, the reasonable parting surface should be selected according to the actual situation of the injection mold.
5. The selection of the mold parting surface should be beneficial to the exhaust
The mold parting surface is the main exhaust channel in the mold structure, and should be set at the end of the plastic melt flow direction as much as possible, and the gating system design should be considered at the same time to facilitate the gas discharge in the mold cavity.
6. The selection of the mold parting surface should consider the lateral core pulling of the mold.
In order to ensure the easy placement of the lateral core and the smooth movement of the core pulling mechanism, when selecting the mold parting surface, the shallow lateral recess or the short lateral boss should be used as the core pulling direction, and the deep recessed hole or the higher boss is placed in the direction of the mold clamping, and the lateral core pulling mechanism is prevented from being placed on the side of the movable mold.
Welcome to ACO Mold injection molding manufacturer and contact us to get free quote.
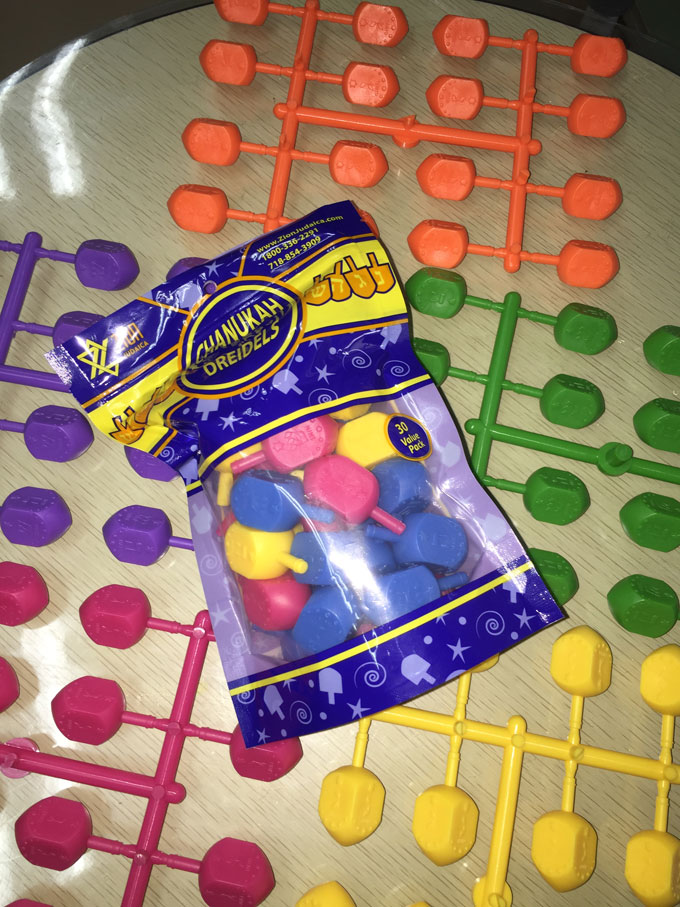
1. The mold parting surface should be located at the maximum contour of the plastic part.
After the orientation of the plastic parts on the moving mold and the fixed mold is determined, the mold parting surface should be located at the maximum contour of the plastic part, otherwise the plastic parts will not be able to demold from the mold cavity. This is the most basic principle of selecting parting surface.
2. The selection of the mold parting surface should be beneficial to the smooth release of the plastic part.
Since the ejection device of the injection molding machine is on one side of the movable mold, the mold parting surface should be selected to ensure that the plastic part remains on one side of the movable mold after mold opening. This facilitates the operation of the push-out mechanism provided in the movable mold portion. If the ejection mechanism is set in the fixed mold, the complexity of the plastic mold will be increased.
3. The selection of the mold parting surface should ensure the accuracy of the plastic parts and the appearance quality.
The mold parting surface cannot be set on the smooth surface and the appearance surface of the plastic product, so as to avoid affecting the appearance quality of the injection molded part.
For parts where the plastic parts require high concentricity, when selecting the mold parting surfaces, it is best to place them in the same side cavity of the injection mold.
4. The selection of mold parting surface should be beneficial to the plastic injection mold making
Usually in the mold structure design, the selection of the straight parting surface is mostly. However, in order to facilitate the injection mold manufacturing, the reasonable parting surface should be selected according to the actual situation of the injection mold.
5. The selection of the mold parting surface should be beneficial to the exhaust
The mold parting surface is the main exhaust channel in the mold structure, and should be set at the end of the plastic melt flow direction as much as possible, and the gating system design should be considered at the same time to facilitate the gas discharge in the mold cavity.
6. The selection of the mold parting surface should consider the lateral core pulling of the mold.
In order to ensure the easy placement of the lateral core and the smooth movement of the core pulling mechanism, when selecting the mold parting surface, the shallow lateral recess or the short lateral boss should be used as the core pulling direction, and the deep recessed hole or the higher boss is placed in the direction of the mold clamping, and the lateral core pulling mechanism is prevented from being placed on the side of the movable mold.
Welcome to ACO Mold injection molding manufacturer and contact us to get free quote.
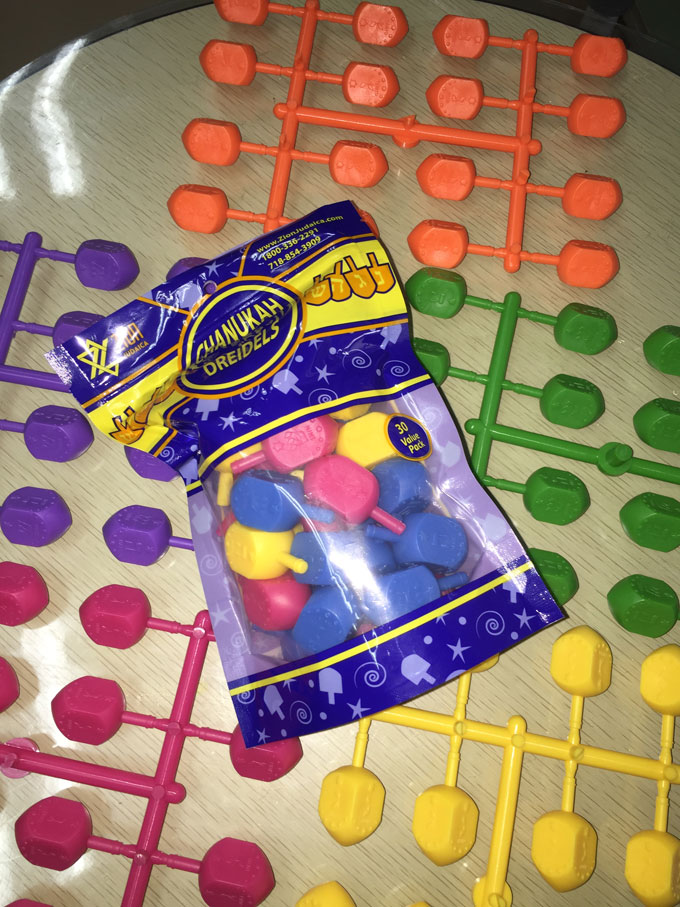