Injection molded plastic parts made in China
Injection molded plastic parts refer to various plastic products processed by plastic injection mold combined with injection molding equipment, including finished and semi-finished plastic products. The injection molding process of plastic parts is based on the type of plastic (thermoplastic or thermosetting), the shape and dimension of injection molded plastic parts etc. The plastic molding process generally use injection molding, blow molding, extrusion etc. Among them, the injection molding is mostly common.
The main molding process parameters of the injection molded plastic parts include:
1. Barrel temperature
The melt temperature is very important, and the temperature of the barrel used is only indicative. The melt temperature can be measured at the nozzle or measured using air jets. The temperature setting of the barrel depends on the melt temperature, screw speed, back pressure, shot volume and injection molding cycle. If injection molding factory have no experience in processing a particular grade of plastic, start with the lowest setting. For ease of control, the barrel is zoned, but not all are set to the same temperature. If operating for a long time or at high temperatures, set the temperature in the first zone to a lower value, which will prevent the plastic from premature melting and shunting. Before plastic molding, make sure that the hydraulic oil, hopper closure, plastic mold and barrel are at the correct temperature.
2. Melt temperature
The melt temperature plays a major role in the flow properties of the melt. Since the plastic has no specific melting point (the so-called melting point is a temperature range in a molten state), and the structure and composition of the plastic molecular chain are different, so the influence of melt temperature on the flow properties of plastic is also different accordingly. The rigid molecular chain is more affected by temperature, such as PC, PPS, etc., while the mobility of flexible molecular chains such as PA, PP, PE, etc. is not obvious by changing the temperature, so it should be adjusted according to different materials.
3. Mold temperature
Some plastic materials require relatively high mold temperature due to the high crystallization temperature and low crystallization speed. Some require higher temperature or lower temperature due to the controlled size and the deformation, or the need for demolding, such as PC, the mold temperature is generally required to be more than 60 Celsius degrees. In order to achieve better appearance of injection molded parts and improve fluidity of plastic, the mold temperature of pp injection molded parts need to be more than 160 Celsius degrees. So the mold temperature has an invaluable effect on improving the appearance, deformation, and size of plastic parts.
4. Injection pressure
The melt overcomes the resistance of advancement, directly affecting the size, weight and deformation of the plastic product. Different injection molded plastic products require different injection pressures. For materials such as PA and PP, increasing the pressure will obviously improve the fluidity of plastic. Injection pressure determines the density of the plastic product, that is, the appearance gloss of the injection molded plastic product. Injection pressure does not have a fixed value. And if the feeding is difficult, the injection pressure should be increased accordingly.
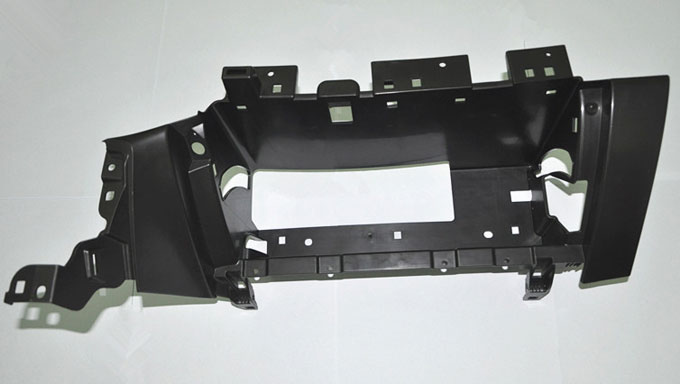
The output of Chinese injection molded plastic parts is in the forefront of the world rankings
Compared with metal, stone and wood, plastic have the advantages of low processing cost and strong plasticity. They are widely used in the Chinese economy. The plastics industry plays an extremely important role in the world today. The large volume injection molding of plastic products has been developing at high speed in the world for many years. Statistics show that the output of injection molded plastic parts mad in China is in the forefront of the world rankings. China has become the world's largest manufacturer of plastic products.
On the basis of the breakthrough in the cutting-edge technology of the plastics industry, China will focus on the key technologies of the core commonalities and strive to narrow the gap of high-tech production technologies with the European and the American countries. The acceleration of technological advancement will give plastic materials and plastic products more and more new functions to meet the needs of the Chinese national economy.
Digital intelligent technology is a common enabling technology for product innovation and manufacturing technology innovation, and they profoundly affect the production mode and industrial form of the Chinese plastic products manufacturing industry.
In the future, the use of lightweight materials in the automotive, aircraft, and rail transit industries will become more and more extensive. Precision injection molding is an embodiment of advanced plastic molding technology, which is of great significance to the plastic industry.
New development trends of Chinese injection molded plastic parts manufacturers
From the injection molding process, the core plastic molding process, such as gas-assisted injection molding, structural foam molding, reaction injection molding, co-injection molding, push-pull molding, injection-compression molding, low-pressure injection molding, alternating injection molding, melt injection molding, dynamic pressure holding Injection molding etc greatly enriched the content of traditional injection molding process, and made the flow properties of plastics, mechanical properties and appearance quality of plastic injection molding products have been effectively controlled.
From the injection molding equipment, in addition to the improvement of traditional injection molding equipment to adapt to the new injection molding process, the injection molding auxiliary machinery automation, energy-saving injection molding machine technology and mold technology, and the development of special injection molding machines have also been greatly improved. For example, the all-electric injection molding machine is a very powerful injection molding machine, which is gradually being promoted at this stage in China.
In addition, computer technology supporting injection molding has also made great progress. For example, computer-aided engineering technology is used for flow state analysis, temperature field analysis, product residual stress analysis, warpage and shrinkage deformation analysis of injection molded plastic parts.
The vigorous development of the injection molding industry is inseparable from the supply of upstream raw materials, and the international raw material market is turbulent. As an injection molding manufacturer, it is necessary to pay close attention to the direction of the international raw material market.
We are Chinese injection molding factory located in Shenzhen Guangdong. We have the strong ability to custom plastic injection molds for your plastic products. If your products are still in the concept stage, Contact Us. And you only need to present your ideas, product features and appearance requirements, the mold engineers from ACO Mold injection molding manufacturer will give you the best solution to help you take the lead in the market. We are ready and looking forward to cooperate with your next project.
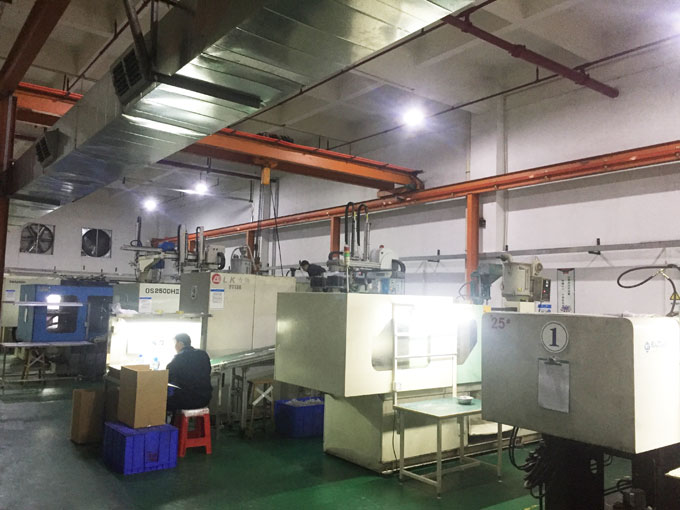
The main molding process parameters of the injection molded plastic parts include:
1. Barrel temperature
The melt temperature is very important, and the temperature of the barrel used is only indicative. The melt temperature can be measured at the nozzle or measured using air jets. The temperature setting of the barrel depends on the melt temperature, screw speed, back pressure, shot volume and injection molding cycle. If injection molding factory have no experience in processing a particular grade of plastic, start with the lowest setting. For ease of control, the barrel is zoned, but not all are set to the same temperature. If operating for a long time or at high temperatures, set the temperature in the first zone to a lower value, which will prevent the plastic from premature melting and shunting. Before plastic molding, make sure that the hydraulic oil, hopper closure, plastic mold and barrel are at the correct temperature.
2. Melt temperature
The melt temperature plays a major role in the flow properties of the melt. Since the plastic has no specific melting point (the so-called melting point is a temperature range in a molten state), and the structure and composition of the plastic molecular chain are different, so the influence of melt temperature on the flow properties of plastic is also different accordingly. The rigid molecular chain is more affected by temperature, such as PC, PPS, etc., while the mobility of flexible molecular chains such as PA, PP, PE, etc. is not obvious by changing the temperature, so it should be adjusted according to different materials.
3. Mold temperature
Some plastic materials require relatively high mold temperature due to the high crystallization temperature and low crystallization speed. Some require higher temperature or lower temperature due to the controlled size and the deformation, or the need for demolding, such as PC, the mold temperature is generally required to be more than 60 Celsius degrees. In order to achieve better appearance of injection molded parts and improve fluidity of plastic, the mold temperature of pp injection molded parts need to be more than 160 Celsius degrees. So the mold temperature has an invaluable effect on improving the appearance, deformation, and size of plastic parts.
4. Injection pressure
The melt overcomes the resistance of advancement, directly affecting the size, weight and deformation of the plastic product. Different injection molded plastic products require different injection pressures. For materials such as PA and PP, increasing the pressure will obviously improve the fluidity of plastic. Injection pressure determines the density of the plastic product, that is, the appearance gloss of the injection molded plastic product. Injection pressure does not have a fixed value. And if the feeding is difficult, the injection pressure should be increased accordingly.
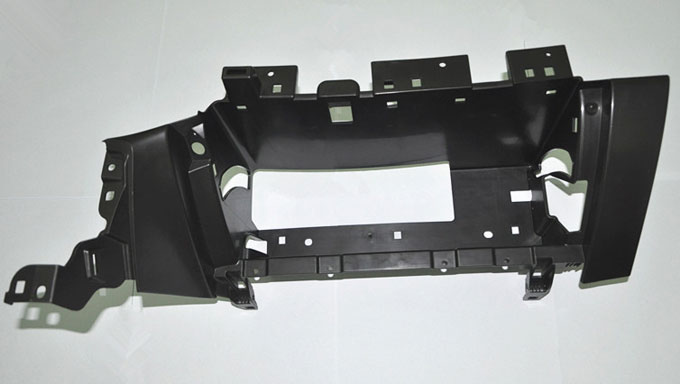
The output of Chinese injection molded plastic parts is in the forefront of the world rankings
Compared with metal, stone and wood, plastic have the advantages of low processing cost and strong plasticity. They are widely used in the Chinese economy. The plastics industry plays an extremely important role in the world today. The large volume injection molding of plastic products has been developing at high speed in the world for many years. Statistics show that the output of injection molded plastic parts mad in China is in the forefront of the world rankings. China has become the world's largest manufacturer of plastic products.
On the basis of the breakthrough in the cutting-edge technology of the plastics industry, China will focus on the key technologies of the core commonalities and strive to narrow the gap of high-tech production technologies with the European and the American countries. The acceleration of technological advancement will give plastic materials and plastic products more and more new functions to meet the needs of the Chinese national economy.
Digital intelligent technology is a common enabling technology for product innovation and manufacturing technology innovation, and they profoundly affect the production mode and industrial form of the Chinese plastic products manufacturing industry.
In the future, the use of lightweight materials in the automotive, aircraft, and rail transit industries will become more and more extensive. Precision injection molding is an embodiment of advanced plastic molding technology, which is of great significance to the plastic industry.
New development trends of Chinese injection molded plastic parts manufacturers
From the injection molding process, the core plastic molding process, such as gas-assisted injection molding, structural foam molding, reaction injection molding, co-injection molding, push-pull molding, injection-compression molding, low-pressure injection molding, alternating injection molding, melt injection molding, dynamic pressure holding Injection molding etc greatly enriched the content of traditional injection molding process, and made the flow properties of plastics, mechanical properties and appearance quality of plastic injection molding products have been effectively controlled.
From the injection molding equipment, in addition to the improvement of traditional injection molding equipment to adapt to the new injection molding process, the injection molding auxiliary machinery automation, energy-saving injection molding machine technology and mold technology, and the development of special injection molding machines have also been greatly improved. For example, the all-electric injection molding machine is a very powerful injection molding machine, which is gradually being promoted at this stage in China.
In addition, computer technology supporting injection molding has also made great progress. For example, computer-aided engineering technology is used for flow state analysis, temperature field analysis, product residual stress analysis, warpage and shrinkage deformation analysis of injection molded plastic parts.
The vigorous development of the injection molding industry is inseparable from the supply of upstream raw materials, and the international raw material market is turbulent. As an injection molding manufacturer, it is necessary to pay close attention to the direction of the international raw material market.
We are Chinese injection molding factory located in Shenzhen Guangdong. We have the strong ability to custom plastic injection molds for your plastic products. If your products are still in the concept stage, Contact Us. And you only need to present your ideas, product features and appearance requirements, the mold engineers from ACO Mold injection molding manufacturer will give you the best solution to help you take the lead in the market. We are ready and looking forward to cooperate with your next project.
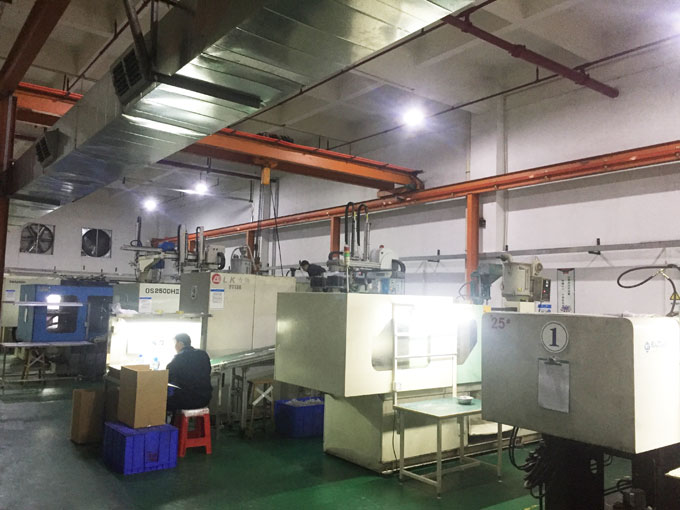