Influence of Injection Molds on Precision Plastic Products Quality
Precision injection molding is affected by many related factors and environmental conditions, and the most basic are the four basic factors of plastic materials, injection molds, injection molding processes and injection molding equipment. In the early stage of designing plastic products, at first, select the engineering plastics that corresponding to the performance requirements according to the application environment. Secondly, selecting the appropriate injection molding machine according to the selected plastic material, the dimensional precision of injection molded parts, the weight of injection molded part, the quality requirements and the expected mold structure. Among the factors related to precision injection molding, injection mold is the key to affect the quality of precision plastic products.
Whether the mold design is reasonable will directly affect the quality of plastic products. The mold cavity size is derived from the required size of the plastic product plus the shrinkage of the material used, the shrinkage rate is often a value within the range recommended by the plastics manufacturer or engineering plastics manual. It is not only related to the gate type, the gate location and the distribution, but the crystal orientation (anisotropic) of engineering plastic, the shape and size of plastic product, the distance from plastic to gate, and the position of gate. The main factors affecting the shrinkage of plastics include heat shrinkage, phase change shrinkage, orientation shrinkage, compression shrinkage and elastic recovery, etc., which are related to the molding conditions or operating conditions of precision injection molded products. Therefore, the injection mold designer must have rich experience in design and injection molding, and must consider the relationship between these influencing factors and injection molding conditions, such as the influence of these factors of injection pressure and cavity pressure and filling speed, injection melt temperature and mold temperature, mold structure and gate type and distribution, as well as the cross-sectional area of gate, the thickness of injection molded product, the content of reinforcing filler in the plastic material, the crystallinity and orientation of plastic material etc. The influence of the above factors also differs depending on the plastic material or other molding conditions such as temperature, humidity, continued crystallization, internal stress after molding, and changes in the injection molding machine.
Because the injection molding process is the process of converting plastic from solid (powder or pellet) to liquid (melt) to solid (product). From the pellet to the melt, and then from the melt to the injection molded product, the effect of temperature field, stress field, flow field and density field are used. Under the combined action of these fields, different plastics (thermoset or thermoplastic, crystalline or amorphous, reinforced or unreinforced, etc.) have different polymer morphological and rheological properties. Any factors that affect the above-mentioned "field" will affect the physical and mechanical properties, size, shape, precision and appearance quality of plastic products.
Considerations when designing precision injection molds
The intrinsic link between the process factor and the properties, structural form and plastic product of the polymer will be manifested by plastic injection molded parts. Analyzing clearly these intrinsic links, which has great significance for the rational preparation of injection molding process, rational design and manufacturing of molds according to drawings, and even the selection of injection molding equipment. Precision injection molding and ordinary injection molding also differ in injection pressure and injection rate. Precision injection molding often uses high pressure or ultra high pressure injection and high speed injection is to obtain a small molding shrinkage. In view of the above various reasons, in addition to considering the design elements of general molds, the following points must be considered when designing precision injection molds:
1. Use appropriate mold dimensional tolerances
2. Avoid the occurrence of molding shrinkage error
3. Avoid the occurrence of injection molding deformation
4. Avoid the occurrence of demolding deformation
5. To minimize mold manufacturing errors
6. Avoid the occurrence of errors in mold precision
7. Maintain mold precision
Avoid the occurrence of molding shrinkage error. Since the shrinkage rate will changes as the changes of injection pressure, so for the single cavity mold, the cavity pressure in cavity should be uniform. As for the multi-cavity mold, the cavity pressure between the cavities should be small. In the case of single cavity multi-gate or multi-cavity multi-gate, it must be injected at the same injection pressure to make the cavity pressure uniform. So, you must ensure that the gates are balanced. In order to make the cavity pressure in cavity uniform, it is best to keep the pressure at the gate entrance consistent. The equilibrium of the pressure at the gate is related to the flow resistance in the runner. Therefore, the runner should be equalized before the gate pressure reaches equilibrium.
Since the melt temperature and the mold temperature have effect on the actual shrinkage rate, in order to facilitate the determination of the molding conditions, it is necessary to pay attention to the arrangement of the cavities when designing the precision injection mold cavity. Because the molten plastic brings heat into the mold, the temperature gradient of mold generally surrounds the cavity, forming a concentric shape centered on the main runner. Therefore, design measures such as flow runner equalization, cavity arrangement, and concentric circular arrangement centered on the main runner are necessary to reduce the shrinkage error between the cavities, to extend the allowable range of molding conditions, and to reduce costs. The cavity arrangement of precision injection mold should meet the requirements of flow runner equalization and the arrangement centered on the main runner, and the cavity arrangement with the main line as the symmetry line must be adopted.
Since the injection mold temperature has a great influence on the molding shrinkage rate, it also directly affects the mechanical properties of injection molded parts, and also causes various molding defects such as fading on the product surface, so the mold must be kept within the specified temperature range, and make the mold temperature won’t change as change of time. The temperature difference between the cavities of the multi-cavity mold also won’t be change. So, temperature control measures for heating or cooling the mold must be taken in the mold design, and in order to minimize the temperature difference between mold cavities, the design of the temperature control-cooling circuit must be paid attention to. In the cavity and core temperature control loop, there are mainly two connection modes: series cooling and parallel cooling.
Whether the mold design is reasonable will directly affect the quality of plastic products. The mold cavity size is derived from the required size of the plastic product plus the shrinkage of the material used, the shrinkage rate is often a value within the range recommended by the plastics manufacturer or engineering plastics manual. It is not only related to the gate type, the gate location and the distribution, but the crystal orientation (anisotropic) of engineering plastic, the shape and size of plastic product, the distance from plastic to gate, and the position of gate. The main factors affecting the shrinkage of plastics include heat shrinkage, phase change shrinkage, orientation shrinkage, compression shrinkage and elastic recovery, etc., which are related to the molding conditions or operating conditions of precision injection molded products. Therefore, the injection mold designer must have rich experience in design and injection molding, and must consider the relationship between these influencing factors and injection molding conditions, such as the influence of these factors of injection pressure and cavity pressure and filling speed, injection melt temperature and mold temperature, mold structure and gate type and distribution, as well as the cross-sectional area of gate, the thickness of injection molded product, the content of reinforcing filler in the plastic material, the crystallinity and orientation of plastic material etc. The influence of the above factors also differs depending on the plastic material or other molding conditions such as temperature, humidity, continued crystallization, internal stress after molding, and changes in the injection molding machine.
Because the injection molding process is the process of converting plastic from solid (powder or pellet) to liquid (melt) to solid (product). From the pellet to the melt, and then from the melt to the injection molded product, the effect of temperature field, stress field, flow field and density field are used. Under the combined action of these fields, different plastics (thermoset or thermoplastic, crystalline or amorphous, reinforced or unreinforced, etc.) have different polymer morphological and rheological properties. Any factors that affect the above-mentioned "field" will affect the physical and mechanical properties, size, shape, precision and appearance quality of plastic products.
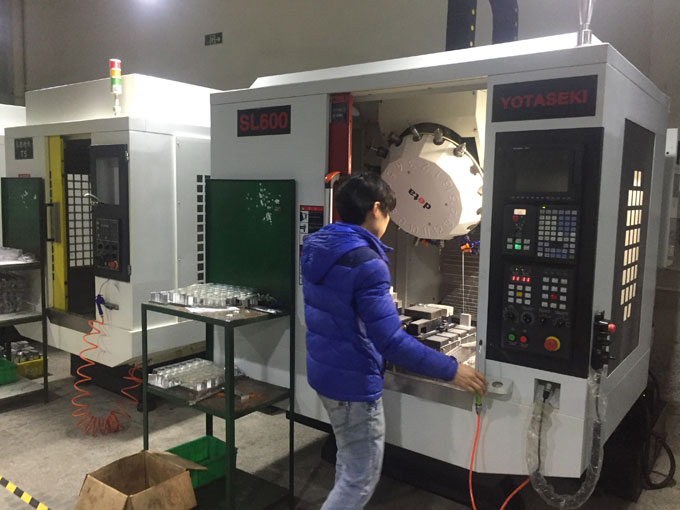
Considerations when designing precision injection molds
The intrinsic link between the process factor and the properties, structural form and plastic product of the polymer will be manifested by plastic injection molded parts. Analyzing clearly these intrinsic links, which has great significance for the rational preparation of injection molding process, rational design and manufacturing of molds according to drawings, and even the selection of injection molding equipment. Precision injection molding and ordinary injection molding also differ in injection pressure and injection rate. Precision injection molding often uses high pressure or ultra high pressure injection and high speed injection is to obtain a small molding shrinkage. In view of the above various reasons, in addition to considering the design elements of general molds, the following points must be considered when designing precision injection molds:
1. Use appropriate mold dimensional tolerances
2. Avoid the occurrence of molding shrinkage error
3. Avoid the occurrence of injection molding deformation
4. Avoid the occurrence of demolding deformation
5. To minimize mold manufacturing errors
6. Avoid the occurrence of errors in mold precision
7. Maintain mold precision
Avoid the occurrence of molding shrinkage error. Since the shrinkage rate will changes as the changes of injection pressure, so for the single cavity mold, the cavity pressure in cavity should be uniform. As for the multi-cavity mold, the cavity pressure between the cavities should be small. In the case of single cavity multi-gate or multi-cavity multi-gate, it must be injected at the same injection pressure to make the cavity pressure uniform. So, you must ensure that the gates are balanced. In order to make the cavity pressure in cavity uniform, it is best to keep the pressure at the gate entrance consistent. The equilibrium of the pressure at the gate is related to the flow resistance in the runner. Therefore, the runner should be equalized before the gate pressure reaches equilibrium.
Since the melt temperature and the mold temperature have effect on the actual shrinkage rate, in order to facilitate the determination of the molding conditions, it is necessary to pay attention to the arrangement of the cavities when designing the precision injection mold cavity. Because the molten plastic brings heat into the mold, the temperature gradient of mold generally surrounds the cavity, forming a concentric shape centered on the main runner. Therefore, design measures such as flow runner equalization, cavity arrangement, and concentric circular arrangement centered on the main runner are necessary to reduce the shrinkage error between the cavities, to extend the allowable range of molding conditions, and to reduce costs. The cavity arrangement of precision injection mold should meet the requirements of flow runner equalization and the arrangement centered on the main runner, and the cavity arrangement with the main line as the symmetry line must be adopted.
Since the injection mold temperature has a great influence on the molding shrinkage rate, it also directly affects the mechanical properties of injection molded parts, and also causes various molding defects such as fading on the product surface, so the mold must be kept within the specified temperature range, and make the mold temperature won’t change as change of time. The temperature difference between the cavities of the multi-cavity mold also won’t be change. So, temperature control measures for heating or cooling the mold must be taken in the mold design, and in order to minimize the temperature difference between mold cavities, the design of the temperature control-cooling circuit must be paid attention to. In the cavity and core temperature control loop, there are mainly two connection modes: series cooling and parallel cooling.