Family injection mold to reduce your mold cost
Usually one finished plastic product consists of more than one component plastic part. To save the mold cost, a family mold is required instead of making one mold for each part. A family mold is a multi-cavity injection mold in which each cavity forms a different part of the finished product.
There are some tips you need to pay attention to:
Production will be much easier if the material and the color are same for each part. This is the most commonly used and most cost-effective combination. All parts come out of the mold at one time, what we need to do is separating the parts after injection molding.
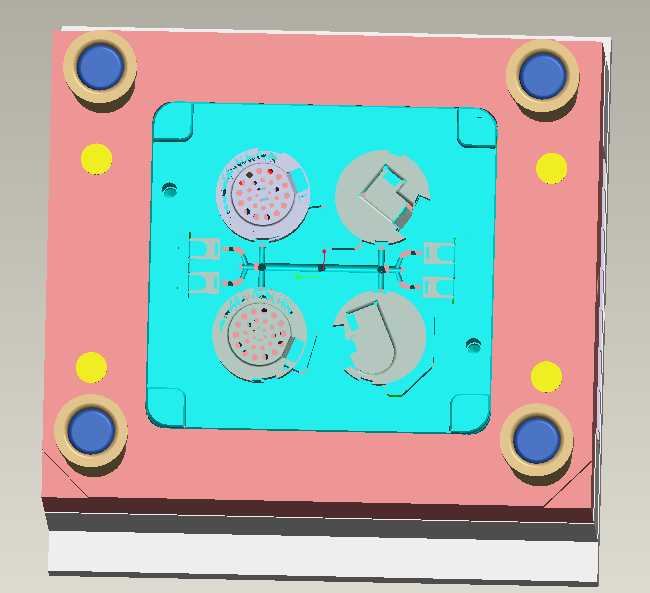
Sometimes different color is required in one finished product for contrast, decoration, etc. Even so, we still can consider a family mold for the parts and make the mold with turntables runner to control the runner shut-off or open. However, the part unit cost will be a little higher because one or multiple of the cavities should be blocked to produce the cavity you want, the productivity is lower. This is a perfect solution for low run production.
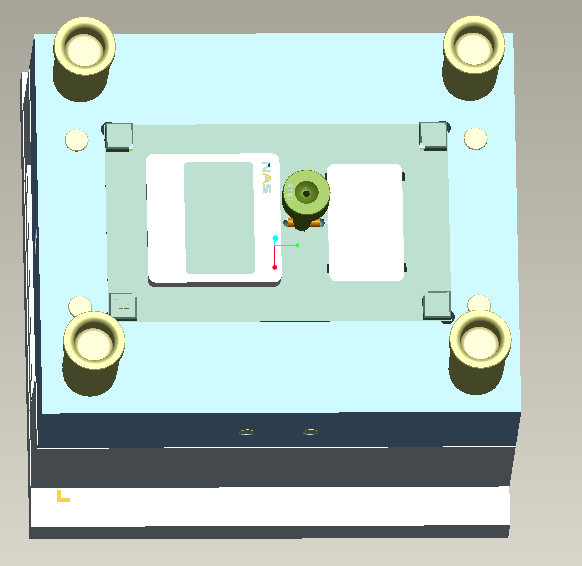
What if different material is required for different function? If the shrinkage rate of the materials is same, we can consider the same way as above, making the mold with turntables runner. However, if the shrinkage rate of the materials is different, we might consider making two blocks in one mold, also with a turnable runner for production.
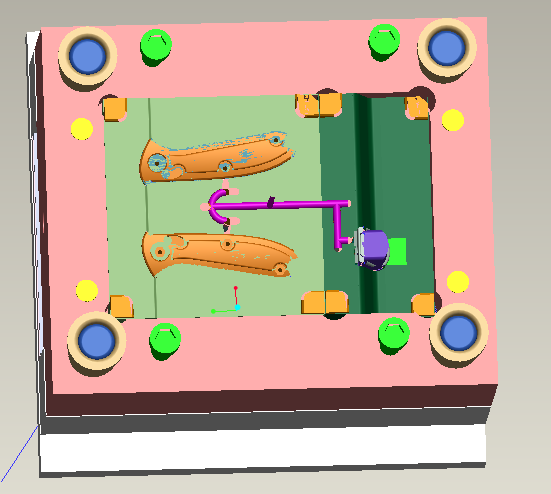
These solutions are not suitable for high volume production. To get a most economical mold solution for your project, contact us now!
There are some tips you need to pay attention to:
- All the parts are supposed to be same material and same color.
- The height of the parts is supposed to be similar, or it might be more expensive than multi cavity mold or single cavity mold.
Production will be much easier if the material and the color are same for each part. This is the most commonly used and most cost-effective combination. All parts come out of the mold at one time, what we need to do is separating the parts after injection molding.
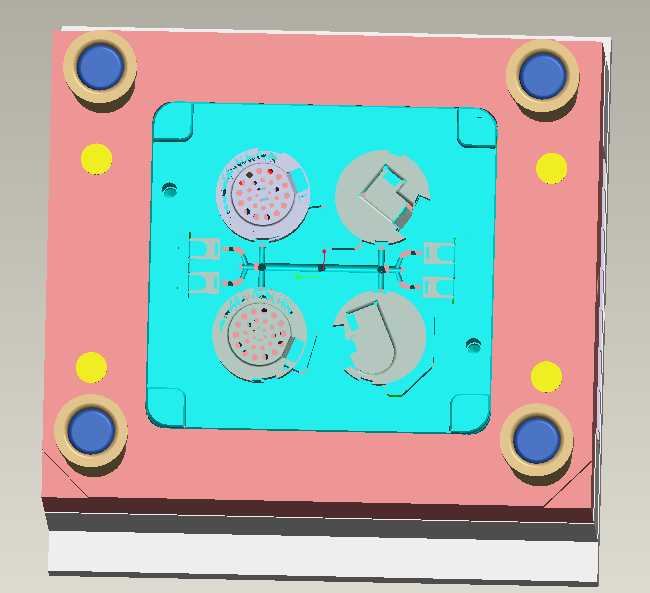
Sometimes different color is required in one finished product for contrast, decoration, etc. Even so, we still can consider a family mold for the parts and make the mold with turntables runner to control the runner shut-off or open. However, the part unit cost will be a little higher because one or multiple of the cavities should be blocked to produce the cavity you want, the productivity is lower. This is a perfect solution for low run production.
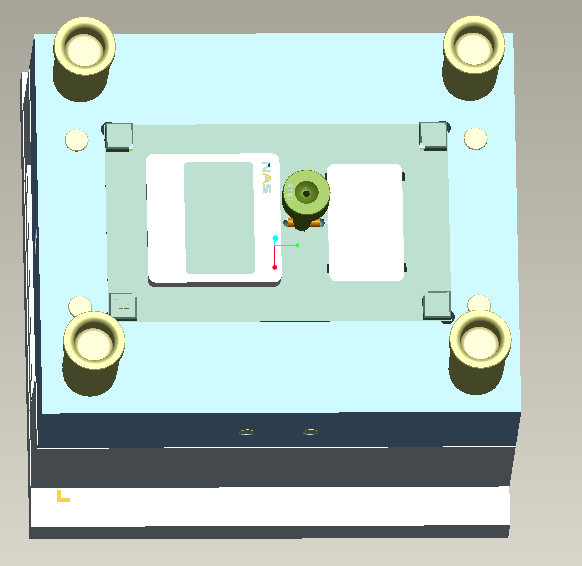
What if different material is required for different function? If the shrinkage rate of the materials is same, we can consider the same way as above, making the mold with turntables runner. However, if the shrinkage rate of the materials is different, we might consider making two blocks in one mold, also with a turnable runner for production.
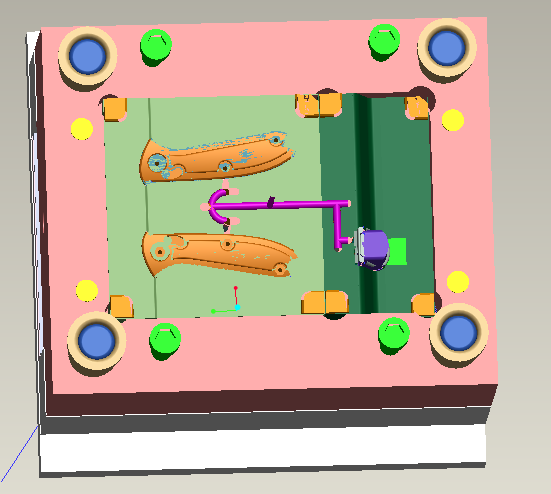
These solutions are not suitable for high volume production. To get a most economical mold solution for your project, contact us now!