Plastic Injection Mold Cost Analysis
Rapid Plastic Injection Mold Cost Calculation
Mold price = materials cost + design cost + processing cost and profit + VAT + tryout cost + packing and shipping costs
The typical ratio is:
Materials cost: materials and standard parts proportion are 15% - 30% of total cost;
Processing cost and profits: 30% - 50%;
Designing cost: 10% - 15% of total cost;
Tryout: large and medium size molds can be controlled within 3%, small precision molds within 5%;
Packing and shipping costs: according to the actual calculation or by 3% of total cost;
VAT: 17%
Plastic Injection Molding Cost Analysis
The cost calculation is based on my own experience in Shenzhen, China:
Injection molded parts cost = plastic material cost + processing cost + packing cost + shipping cost
Which:
Material cost = [(1 + plastic material loss) * product weight * Batch + debug material lost weight + normal rejection rate * product weight * Batch] * Material Unit Price / Batch.
Where the plastic material loss is 3% -5% generally; general products of debug material lost weight and normal rejection weight is 5000g - 15000g.
Processing cost = (debug time / batch + molding time / mold cavities) * plastic injection molding machine processing costs
Which as far as I know, the plastic injection molding machine processing costs in Shenzhen region are differ by the tonnage of the injection molding machine (China made equipment).
Injection Molded Parts Cost Calculation
Product Unit Price = material cost + processing costs
Material cost = (actual weight + loss weight) * Material Unit Price
Processing cost = molding cycle * Price (s) ÷ cavity number (means the price of each part)
For special packaging requirements, add packaging costs.
When you send an RFQ, it's important to share as many as possible with your supplier. Each of the injection molded parts project are custom made to meet individual company's requirements. Here are few points:
The drawings
It's best to provide drawings in 2D and 3D format, these are accuracy information that tell some important factors such as part weight, molding cycle, mold making concerns.
The target price
Cost objectives could be achieved by eliminating unnecessary design or non-value-added items. Suppose you need 20,000 plastic parts, do you need these plastic parts for life of this project? Or do you need 20000 for the first stage and more for the next? The injection molder / mold maker base on different requirements will provide different solutions.
The time
Let the injection mold maker know the schedule so they can plan the production well, nothing is rush or fall behind.
The sample time?
The first batch of molded parts for testing?
The mass production time?
The surface requirement
The surface requirement will influence plastic injection mold design, such as gate location, parting line or inserts, ejection, your supplier will need such information to decide the most economic mold design.
The materials
Material selection depends on the requirement of the plastic parts, your injection molding factory should be able to propose alternative material to reduce plastic part cost.
The required quantity
It's quit critical to give the expected volumes, it will affect the plastic injection mold making cost, plastic part cost.
Mold price = materials cost + design cost + processing cost and profit + VAT + tryout cost + packing and shipping costs
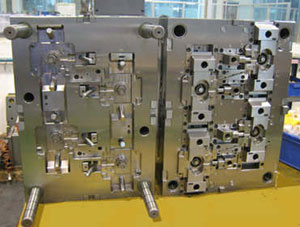
Materials cost: materials and standard parts proportion are 15% - 30% of total cost;
Processing cost and profits: 30% - 50%;
Designing cost: 10% - 15% of total cost;
Tryout: large and medium size molds can be controlled within 3%, small precision molds within 5%;
Packing and shipping costs: according to the actual calculation or by 3% of total cost;
VAT: 17%
Plastic Injection Molding Cost Analysis
The cost calculation is based on my own experience in Shenzhen, China:
Injection molded parts cost = plastic material cost + processing cost + packing cost + shipping cost
Which:
Material cost = [(1 + plastic material loss) * product weight * Batch + debug material lost weight + normal rejection rate * product weight * Batch] * Material Unit Price / Batch.
Where the plastic material loss is 3% -5% generally; general products of debug material lost weight and normal rejection weight is 5000g - 15000g.
Processing cost = (debug time / batch + molding time / mold cavities) * plastic injection molding machine processing costs
Which as far as I know, the plastic injection molding machine processing costs in Shenzhen region are differ by the tonnage of the injection molding machine (China made equipment).
Injection Molding Machine (T) |
Cost (Yuan/hour) |
Injection Molding Machine (T) |
Cost (Yuan/hour) |
80 |
35 - 45 |
200 |
110 - 160 |
100 |
45 - 60 |
250 |
150 - 200 |
120 |
65 - 85 |
300 |
180 - 220 |
150 |
80 - 110 |
350 |
200 - 250 |
180 |
95 - 140 |
400 |
250 - 350 |
Injection Molded Parts Cost Calculation
Product Unit Price = material cost + processing costs
Material cost = (actual weight + loss weight) * Material Unit Price
Processing cost = molding cycle * Price (s) ÷ cavity number (means the price of each part)
For special packaging requirements, add packaging costs.
When you send an RFQ, it's important to share as many as possible with your supplier. Each of the injection molded parts project are custom made to meet individual company's requirements. Here are few points:
The drawings
It's best to provide drawings in 2D and 3D format, these are accuracy information that tell some important factors such as part weight, molding cycle, mold making concerns.
The target price
Cost objectives could be achieved by eliminating unnecessary design or non-value-added items. Suppose you need 20,000 plastic parts, do you need these plastic parts for life of this project? Or do you need 20000 for the first stage and more for the next? The injection molder / mold maker base on different requirements will provide different solutions.
The time
Let the injection mold maker know the schedule so they can plan the production well, nothing is rush or fall behind.
The sample time?
The first batch of molded parts for testing?
The mass production time?
The surface requirement
The surface requirement will influence plastic injection mold design, such as gate location, parting line or inserts, ejection, your supplier will need such information to decide the most economic mold design.
The materials
Material selection depends on the requirement of the plastic parts, your injection molding factory should be able to propose alternative material to reduce plastic part cost.
The required quantity
It's quit critical to give the expected volumes, it will affect the plastic injection mold making cost, plastic part cost.
I have really enjoyed your article, thank you for taking the time for putting this kind of article in the web that people could used and learn more about real cost that are involved in right pricing either directly or indirectly for injection molding parts.
I would really appropriated if you can help me littler more to better understand what you mean by "Batch" and "debug time and "debug material"?
I would like to thank you in advance for your time and your help in this matter.
Thank you so much,
Eddie