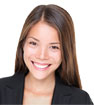
Mold Manufacturer China

How does an injection molding plant operate? I believe many people have thought about this issue and want to learn about this issue. Now I will try to tell you about this unknown world and talk about the day-to-day operations of the factory.
Stamping die is a kind of special process equipment that processes material (metal or non-metal) into parts (or semi-finished products) in cold stamping process, which is called cold stamping die (commonly known as cold die). What’s more stamping is a pressure processing method that uses a mold mounted on a press to apply pressure to a material at room temperature to cause separation or plastic deformation, thereby obtaining a desired part. In additions to this dies and presses are the two key factors that determine the quality, accuracy, and productivity of stamping. Only advanced molds can be used in advanced presses to make full use of them and achieve good results.
In the metal mold industry, the market for molds grows. With the establishment of industrial parks for molds across the country, China's mold industry has gained market recognition and rapid development. In mid-to-high-end production, it has also been able to achieve higher-level upgrades and jumps from the earliest stages of development. , injection mold or other are also gradually developed.
Injection molds generally need to work in a high temperature environment of 150 to 200 degrees Celsius when manufacturing plastic products in an injection molding machine. Therefore, the selection of raw materials in the process of manufacturing injection molds requires great attention, which plays a crucial role in the later overall injection mold life and the quality of the production of plastic products. And then, in the selection of injection mold steel raw materials need to meet what performance requirements?
The price of export mold is more expensive due to the different standards. The mold is divided into five categories by SPIAN-102-78. Five types of mold have different requirements and standards of themselves. This kind of mold classification only applies to the mold of injection molding machine with 400 tons or less.
Processing enterprises should be in the injection molding machine, injection mold under normal operation, test all kinds of injection mold performance, and finally measure forming parts size, through these information can determine the existing state of injection mold, find out the cavity, core, cooling system and parting surface damage, according to the information provided by the plastic, can judge the injection mold damage status and maintenance measures.
There are many factors to influence the injection mold cooling,such as the shape of plastic parts,and the parting surface design, the types, temperature and flow rate of cooling medium, geometry parameters and spatial arrangement of cooling pipe, mold material, melt temperature, eject and mold temperature that plastic parts requiring, thermal cycling interaction between plastic parts and molds,etc.
Four matters needing attention of maintenance of injection mould.
According to concerning sectional statistic, at present, China has been built and begun to take shape of the injection mold industrial park have nearly one hundred or so, there are some injection mold industrial park is under the construction planning. We believe that China will develop into the world injection mold manufacturing center in the future.
Most of my injection experience is in optical lens, so stress (optical birefringence) is visible and to be avoided. We molded opthalmic lenses and magnifiers so we had high aspect ratio parts. We measured part deformation with a Wyco. We also added dyes to the products, mixing in the injection molding extruder only.
To me the key is getting the resin into the injection mold quickly, slowing cooling to the Tg all the part and then cooling it slowly down to room temperature. If there was a way to injection a warm injection mold and then bring the temperature of the part down slowly and evenly at first and then speed it up this would be an asset. Naturally I have considered other ideas over the years. Air cooling could allow an on off approach to cooling, but I have set up a PET tape process with just air drying after the bath and the volume of high pressure air required to get significant cooling is costly.
To me the key is getting the resin into the injection mold quickly, slowing cooling to the Tg all the part and then cooling it slowly down to room temperature. If there was a way to injection a warm injection mold and then bring the temperature of the part down slowly and evenly at first and then speed it up this would be an asset. Naturally I have considered other ideas over the years. Air cooling could allow an on off approach to cooling, but I have set up a PET tape process with just air drying after the bath and the volume of high pressure air required to get significant cooling is costly.
It depends on several factors.
- You can work with the same mold, but you need to consider what happening with the cavity surface, due to a great friction inside if try a 50% of G.F., your mold must be have a surface treatments, or special finishing protection, also some time is better use special oil.
- If the sink marks is continuously you can try to improve some special test runs into the injection molding machine process, I recommend you try with 3-4 different profiles at the second pressure in order to led the flow front advance and fill the cavities more properly.
- The data of the material that you are using is around of: Linear mold shrink for PA66+30GF 0.2-0.6%
Melt temperature 428-579 °F
Mold temp. 104-140°F
Linear mold shrink for PA66+50GF 0.09-0.11%
Melt temperature 455-590 °F
Mold temp. 104-140°F
It is bit unfortunate that the injection molding machines have made so many advances whilst the mold- where all the action happens remains in 17th century- apart from using CNC technology that makes it more accurate reproduction of CAD file. Cooling is by and large after thought, where can I put some cooling lines? Radiator in a car is not an option, car will not run without one and why our molds have an afterthought for radiator? How many tool specifications define no. of shots to tool stabilization? Uniformity of temperature over entire part (just take a simple thermal image of any part after injection molding and see how bad the variation is). Parts vary in quality and have warpage not so much because melt is having some variation in couple of degrees C, when tool has hot spots and delta T in excess of 60 Deg. C.
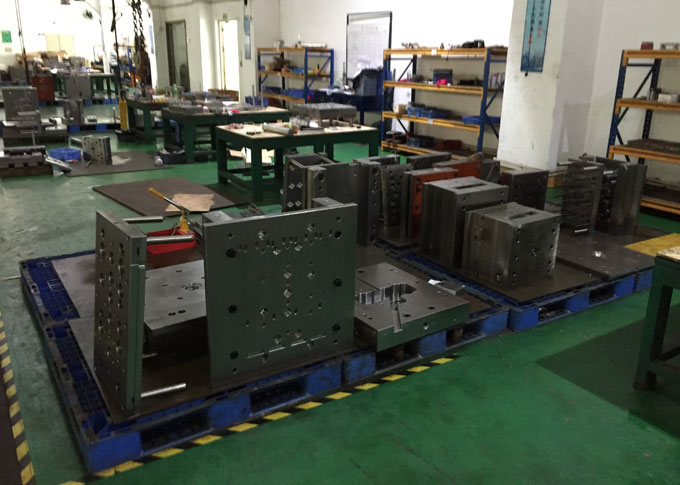
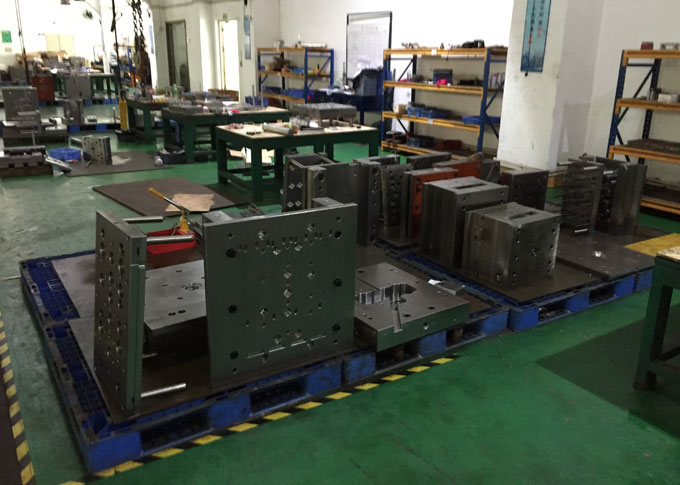