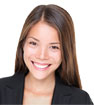
Mold Manufacturer China

Injection molded plastic parts refer to various plastic products processed by plastic injection mold combined with injection molding equipment, including finished and semi-finished plastic products. The injection molding process of plastic parts is based on the type of plastic (thermoplastic or thermosetting), the shape and dimension of injection molded plastic parts etc. The plastic molding process generally use injection molding, blow molding, extrusion etc. Among them, the injection molding is mostly common.
In order to make the injection mold precise and high-quality, injection molding manufacturing will heat the injection molds. It can not only improve the precision of the injection molds, but also improve the quality and precision of the injection molded parts. ACO Mold injection molding factory share precautions about heat treatment of plastic injection mold with product companies. There are main 4 sections of forging process, pre-heat treatment, quenching, and temper.
The parting surface is for taking out the injection molded plastic part from the mold cavity or in order to meet the needs of plastic molding, such as the installation of insert, and the exhaust. According to the structure of plastic part, the part of the injection molded part is divided into several parts of touch surface. It is divided into horizontal parting surface, vertical parting surface and composite parting surface. When plastic injection molding, in order to facilitate the release of the injection molded part, the plastic injection mold is made into several parts and the joint surface is called the parting surface. When selecting parting surface, try to ensure the quality of the injection molded plastic parts and simplify the processing process of mold making and injection molding. The selection of the parting surface is also the first step in the mold design. It is affected by many factors such as the shape, appearance, wall thickness, dimensional accuracy, and number of cavities.
The basis for judging precision injection molding is the precision of the injection molded product, that is, the dimensional tolerance, shape tolerance and surface roughness of the plastic product. There are many relevant conditions for precision injection molding, and the most essential are the four basic factors of plastic materials, injection molds, injection molding processes and injection molding equipment. When designing plastic products, engineering plastic materials should be selected first, and engineering plastics capable of precision injection molding must use materials with high mechanical properties, dimensional stability, good creep resistance and environmental stress cracking resistance. Secondly, the appropriate injection molding machine should be selected according to the selected plastic material, the dimensional accuracy of the finished product, the weight of the plastic part, the quality requirements and the expected mold structure. In the process of precision injection molding, the factors affecting precision injection molding products mainly come from the precision of the precision injection mold, the shrinkage of the injection molding, and the variation of the ambient temperature and humidity of the product.
In the past, molds for injection molding were usually made of steel or aluminum, and were manufactured using reduced-material manufacturing techniques, such as CNC machine tools. But more and more companies have recently tried to use more advanced 3D printing processes to simplify the mold making process.
When plastic molding, the temperature of mold cavity is required to reach 300 °C or higher. Such large temperature difference will easily cause that the cavity structure generates microscopic changes, which lead to the change of mold size and the un-stability of the size of plastic part. So, the heat treated steel can be used. In order to improve the hardness and wear resistance, injection mold is generally subjected to heat treatment. We’d better use the pre-hardened steel which has smallest influence on mold size and can be machined by cutting. This steel doesn’t require heat treatment after machining.
The cooling system is also called heat exchange system. When the melt is injected into the cavity, the cooling system cools and condenses the injection molded parts quickly. The economic significance is to shorten the molding cycle and improve the production efficiency. The design of cooling system is often limited by the geometry of cavity (mold cavity), the parting line, the slider and the ejector rod. Therefore, it cannot be rigidly designed according to the standard distribution. The cooling system must be designed to ensure rapid and uniform cooling.
(1) Exclude the air in the cavity when injecting the molten material
(2) Exclude various gases generated during the heating process. The thinner the wall of molded part, the farther away from the gate, the more important the setting of air vent. In addition, for small parts or precision parts, the setting of air vent is also should be paid attention. Because it can avoid the surface burns of injection molded part and insufficient injection volume, and can also eliminate various defects of molded product and reduce mold pollution, etc. So, how to know that the exhaust of cavity is sufficient? In general, if the melt is injected at the highest injection rate without leaving a focal spot on the injection molded part, it can be considered that the exhaust in the cavity is sufficient.
(2) Exclude various gases generated during the heating process. The thinner the wall of molded part, the farther away from the gate, the more important the setting of air vent. In addition, for small parts or precision parts, the setting of air vent is also should be paid attention. Because it can avoid the surface burns of injection molded part and insufficient injection volume, and can also eliminate various defects of molded product and reduce mold pollution, etc. So, how to know that the exhaust of cavity is sufficient? In general, if the melt is injected at the highest injection rate without leaving a focal spot on the injection molded part, it can be considered that the exhaust in the cavity is sufficient.
The standard mold base generally consists of the fixed clamp plate of upper mold, the fixed mold plate, the movable mold plate of lower mold, the movable mold support plate, the padding block, the moving clamp plate, the push bar fixing plate, the stripper plate, the guide pin, the guide bush and the reset lever and so on. In addition, there are some mold bases with special structure, such as point gate mold base, mold base with stripper plate push out, etc. Other parts of the mold base can be supplemented as needed, such as precision positioning devices, supporting columns and other accessories. Basically, the accessories need to be used are already including in the standard mold base.
The mechanical arm during injection molding is generally composed of execution system, drive system, control system etc. The execution and drive system is designed to perform the normal functioning of mechanical arm. Driving mechanical parts by pneumatic or electric motor to reach the function of taking out objects. With the wide application of mechanical arm, insert, shear products glue and simply assemble are more convenient.
The accuracy concept is the basic concept and consciousness that mold designers must establish. Mold accuracy includes overall mold assembly and zero and component position and shape dimensional accuracy, mating accuracy, and positioning accuracy. Such as die punching gap value and uniformity, plastic injection mold, die casting mold positioning and positioning accuracy, etc., need to be the shape of the punch and die, position accuracy, guide device position and match accuracy.
Therefore, strict dimensional accuracy design and calculation are required in the mold design. At the same time, the manufacturing process and precision of the parts and components must also be considered to ensure the precision of the mold.
Therefore, strict dimensional accuracy design and calculation are required in the mold design. At the same time, the manufacturing process and precision of the parts and components must also be considered to ensure the precision of the mold.
In recent years, the manufacturing industry has become more and more fierce in the world, and the ability to provide customers with high-quality products with high efficiency and low consumption in the shortest possible time has become a symbol of the competitiveness of companies. The mold is called the father or industry. The quality of the mold will directly affect the quality of the product, its production, its cost, the time it takes for the new product to be put into production and the replacement of the old product, the speed at which the company's product structure is adjusted, and the market's competitiveness. The quality of the mold has raised higher and higher requirements. So how can we improve mold quality more reasonably? In other words, how can we allow the mold to produce quality-qualified parts more accurately and at low cost and high efficiency over a longer period of time and with more modes? This has increasingly become the focus of attention. Mold quality is not a simple topic.